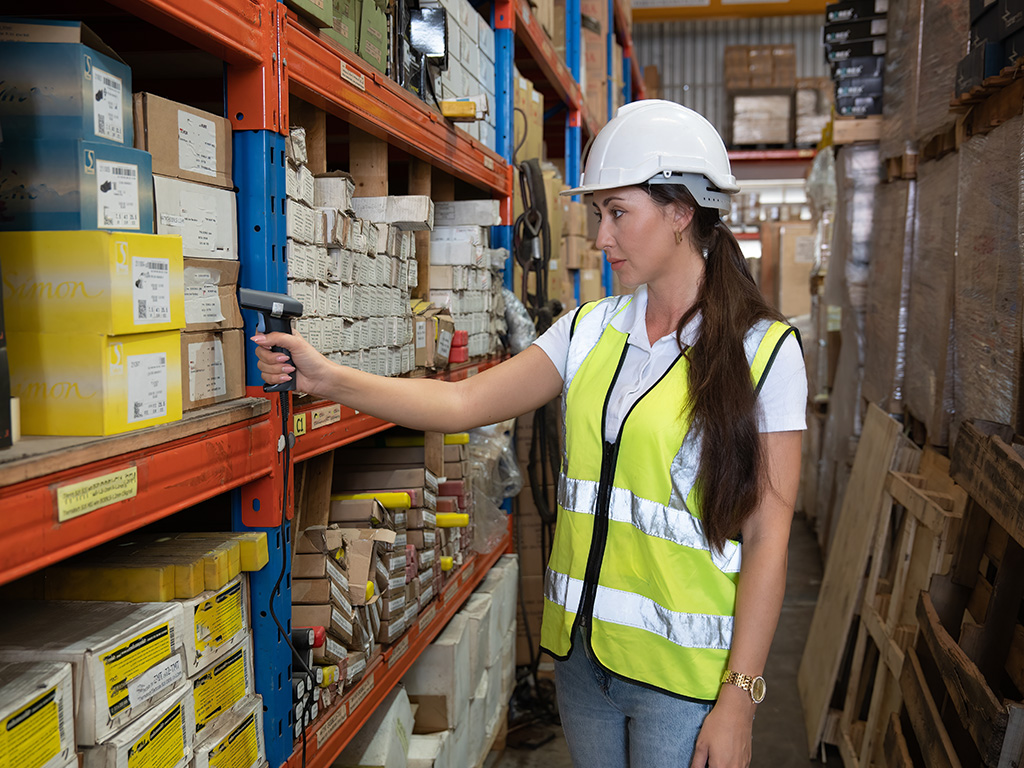
Confirming that all your stock items are present at the right location and in the correct quantities in your warehouse is, at best, labour intensive and non-value adding. At worst, investigation of inaccuracy and loss can require serious amounts of resources to resolve, drain trust from your business if stock is not available for customer orders, and cost your organisation significant amounts of money. It is easy to ignore or forget the importance of stock management until it is too late and the issues are uncovered. So, what is the best way to stay on top of stock accuracy – before it gets on top of you?
Warehouse stock management is an unloved and oft-misunderstood area of warehousing. In regular warehouse operations, there will be losses, miscounting and damage – the question is how much an “acceptable” level of loss in the warehouse is. Of course, the answer is, “it depends” – but on what?
There are several categories of potential loss in a warehouse. Let’s call out the most common:
- Losses on receipt into the warehouse from suppliers, sub-contractors or production sites caused by insufficient checking, mis-identification of stock items, confusion between “Units of Measure”(especially when delivery documentation is unclear on the subject of units, cases, layers and pallet quantities) and sometimes deliberate attempts to deceive (boxes missing from the centre of a pallet stack or ostensibly “full” cases that are missing items) – these are all issues that contribute to stock discrepancies.
- Losses caused by damage in the warehouse through human error, malicious damage, poor packaging: forklift drivers may place pallets unsafely in racking causing a collapse later; pallets can be damaged by collisions during transit; order pickers can drop or damage boxes; loaders can damage goods when placing them onto trucks for despatch.
- Losses caused by mistakes in order assembly: Replenishment stock can be placed in the wrong position; pickers can select from the wrong location; pickers can pick the wrong quantity.
- Losses in transit to the customer or the manufacturing location or a sub-contractor: Poor loading can cause loads to move during transit, or the unloading location can damage goods when unloading them (but claim that they were received in that state).
- Losses incurred at the point of delivery to customers, where a customer claims for damage that may, or may not, have actually occurred.
- Losses in returned product caused by discrepancies between what has been credited to the delivery point and what is actually received back at the warehouse
- Losses caused by theft i.e. stock is physically removed from the warehouse without permission, either opportunistically (for example, stock is left on a vehicle by error) or systematically by dishonest staff colluding to exploit a lack of control in the warehouse.
- “Timing” and “Stock Integrity” issues – temporary misalignment between systems meaning that the warehouse system is showing different stock availability to other systems (for example, if a customer ordering system or Enterprise Resource Planning (ERP) system does not interface with the warehouse system in real time, care must be taken to count stock when all systems are aligned)
- Losses cause by “Act of God” including flooding, lightning strikes and other natural disasters – a catastrophic event that will require special investigation, especially if an insurance claim is involved.
Each of these categories (except the last) will be present in most warehouses at some level. The key is to identify which sources of loss are most important to your warehouse operation by finding evidence of misalignment between the stocks your systems tell you should be in the warehouse and the stock that is actually in the warehouse – before the problem gets out of control.
This can be done in many ways:
- Manual re-checking of receipts and/ or despatches (Physical separation of items and checking manually)
- “Rest case counts” during order assembly (picker counts what is left in a pick face after picking from that location)
- Ad hoc stock checks (for example – count the items in the pick face after picking activities are completed)
- Aisle checks (all locations in a single aisle are checked)
- Empty location checks (all locations expected to be empty of stock are physically checked)
- Item counts responding to shortage claims (all locations of a product that has been reported as “short (or over) delivered” are physically checked)
- System generated counts (Warehouse Management System (WMS) generates requests to check stock according to an algorithm)
- “Perpetual inventory” where all locations are checked within a specified time period (weekly, monthly, quarterly or annual)
- Periodic physical stock checks of all locations at the same time
- Stock integrity checks – ensuring that stock records for two systems (normally the ERP and WMS) are aligned.
Each of these methods of identifying discrepancies have pros and cons. The right method for your warehouse may well be a combination of different methods, tailored to the specific situation and requiring regular reviews to remain in control. Despite this, many organisations rely only on “full” stock counting, as there is often an annual requirement to verify the accuracy of the stock record for the organisation’s financial accounting. Discovery of significant losses and discrepancies during this accounting-led process is a worst-case scenario in stock management. If these counts are only performed annually, semi-annually or even quarterly, the discovery of discrepancies requires investigation of stock movements over a long period of time. This makes identification of root causes more difficult. Moreover, the tolerance, patience and understanding of the organisation’s Chief Financial Officer when significant financial discrepancies are discovered during the end-of-year reporting period is often in extremely short supply!
Unfortunately, all methods of stock management require resources and there is a tendency to drain resources from stock management to support more urgent operational matters. This can be short sighted – good stock management, encompassing regular counting regimes, rapid investigation and clear remedial actions can reduce the risk of customer shortages and improve customer satisfaction.
Heed the tell-tale warning signs that you have a stock management issue: frequent requests to replenish pick locations that should not be empty; frequent claims for missing or incorrect items from customers; frustrated forklift truck drivers reporting that supposedly “empty” locations already contained stock; a build up of “damaged” stock awaiting write off and disposal, a “returns” area overflowing with unprocessed stock…… – these, and others, are signs that Stock management is under pressure and requires attention before the situation escalates out of control.